Fortschritte für die Additive Fertigung
19.06.2023Für ein neues Projekt hat Professor Jürgen Groll rund 880.000 Euro eingeworben. Sein Team will damit die Basis für verbesserte multifunktionale medizinische Implantate und Werkstoffe legen.
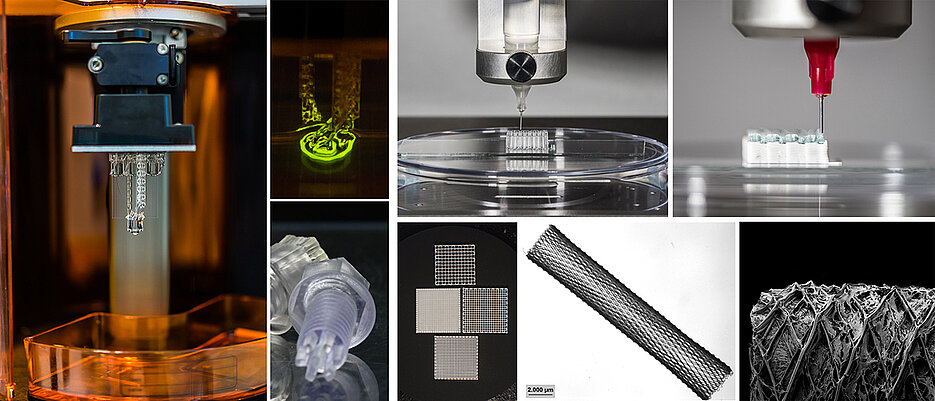
Mit 3D-Druckern lassen sich effizient technische Werkstoffe und medizinische Implantate herstellen. Diese Art von Produktion ist auch unter dem Namen Additive Fertigung bekannt.
Sollen die Produkte aus mehreren Materialien bestehen und mehrere Funktionen ausüben, gibt es aber noch Hürden zu nehmen – Materialeigenschaften müssen aufeinander abgestimmt, die Präzision der Bauteile gesteigert werden. Auch ist es bislang nicht möglich, die Qualität des Fertigungsprozesses schon während des Druckens zu kontrollieren.
Diese Herausforderungen geht ein neues Projekt an der Julius-Maximilians-Universität Würzburg (JMU) an, das mit Unterstützung bei der Erstellung des Projektantrages durch das Servicezentrum Forschung und Technologietransfer (SFT) eingereicht wurde.
Das SFT berät Wissenschaftlerinnen und Wissenschaftler der JMU bei der Beantragung von Mitteln aus den Europäischen Fonds EFRE und ESF. Die Bezeichnung EFRE bedeutet Europäischer Fonds für regionale Entwicklung, ESF steht für Europäischer Sozialfonds. Diese Fonds sind die wichtigsten Instrumente der EU zur Stärkung des wirtschaftlichen, sozialen und territorialen Zusammenhalts.
Geld für zwei wissenschaftliche Personalstellen
Das bayerische Wissenschaftsministerium fördert so Jürgen Grolls Projekt „Maßgeschneiderte Komponenten für die Additive Fertigung multimaterialer Produkte (für Technik und Klinik)“ aus EFRE-Mitteln mit rund 880.000 Euro. Das Vorhaben ist Anfang Mai 2023 an den Start gegangen und läuft vier Jahre; das Fördergeld wird für zwei wissenschaftliche Personalstellen eingesetzt.
Projektleiter Professor Jürgen Groll ist Inhaber des Lehrstuhls für Funktionswerkstoffe der Medizin und der Zahnheilkunde. Sein Team will in Kooperation mit neun kleinen und mittleren Unternehmen Additive Fertigungstechnologien weiterentwickeln.
Worauf das EFRE-geförderte Projekt abzielt
Ein Ziel ist die Implementierung von Algorithmen des maschinellen Lernens, die beim 3D-Druck in Echtzeit Fertigungsfehler erkennen und ihnen sofort gegensteuern, indem sie die Druckparameter anpassen. Das Projektteam strebt auch die Kombination verschiedener Verfahren an, um die Herstellung bislang nicht druckbarer multifunktionaler Werkstücke möglich zu machen. Außerdem sollen für den 3D-Druck maßgeschneiderte neue Polymer- und Keramikwerkstoffe entwickelt werden.
Einsatzgebiete sind unter anderem patientenspezifische Implantate für Hart- und Weichgewebe, etwa im Bereich des Gesichtsschädels, wobei eingedruckte Fasergerüste der mechanischen Verstärkung des Bauteils dienen oder nach dem Herauslösen eine gerichtete Porenstruktur für das Einwachsen von Zellen liefern. Aber auch die Herstellung von Bioreaktoren, in denen die zellbeladenen Gerüste kultiviert werden, können individuell gefertigt werden.
Ein Technologietransfer auch in technische Applikationen, zum Beispiel der additiven Fertigung von porösen keramischen Membranen zu Filter- und Separationszwecken, wird angestrebt.
Beteiligte kleine und mittlere Unternehmen
- Bavaria Filaments, Freilassing
- BioCer Entwicklungs-GmbH, Bayreuth
- Curasan AG, Kleinostheim
- nanoplus Advanced Photonics Gerbrunn GmbH
- HuemmerSeidl GbR / NEROW, Rügheim
- Peter Brehm GmbH, Weisendorf
- ppPrint GmbH, Bayreuth
- TUTOGEN MEDICAL GmbH, Neunkirchen am Brand
- Ingenieurbüro Christian Reil (CR-3D), Cham
15 Jahre Expertise für Additive Fertigung
Am Würzburger Lehrstuhl für Funktionswerkstoffe der Medizin und der Zahnheilkunde besteht eine mehr als 15-jährige Expertise in der Anwendung von 3D-Druck-Verfahren.
Hier werden Additive Fertigungstechniken wie 3D-Pulverdruck, Digital light processing oder Stereolithographie verwendet, um Trägerstrukturen für Zellen, patientenspezifische keramische Implantate und Bioreaktoren für die Zellkultur zu fabrizieren. Der Lehrstuhl deckt die gesamte Fertigungskette ab: das Design der Strukturen, die Entwicklung von Materialien, die für den Druckvorgang maßgeschneidert sind, die Fertigung selbst sowie die Nachbehandlung zur Einstellung der gewünschten Materialeigenschaften.
Das EU-Förderprogramm EFRE
Das Förderprogramm EFRE der Europäischen Union unterstützt Projekte zum Technologietransfer zwischen Hochschulen und kleinen und mittleren Unternehmen (KMU). Forschende sollen die Unternehmen bei aktuellen Fragestellungen unterstützen – mit dem Ziel, weitere Innovationen in KMU anzuregen und diese auf einem sich entwickelnden Markt früh in eine Position als Technologieführer zu bringen.
Kontakt
Lehrstuhl für Funktionswerkstoffe der Medizin und der Zahnheilkunde: https://www.fmz.uni-wuerzburg.de/